The advent of Industry 4.0, characterized by the fusion of advanced manufacturing techniques with the Internet of Things (IoT), artificial intelligence (AI), and data analytics, is transforming the industrial landscape. At the heart of this revolution are Programmable Logic Controllers (PLCs), which are pivotal in automating and optimizing industrial processes. This has revolutionized the automation industry all the way and this is really considered as a game changer in industry.
The Evolution of PLCs
PLCs have been a cornerstone of industrial automation since their inception in the late 1960s. Initially developed to replace relay-based control systems, PLCs provided a more flexible, reliable, and efficient means of control. Over the decades, PLCs have evolved significantly, incorporating more advanced features and capabilities. Today, modern PLCs are equipped with high-speed processors, extensive memory, and enhanced connectivity options, making them indispensable in the era of Industry 4.0.
Key Roles of PLCs in Industry 4.0
-
Enhanced Connectivity and Integration: PLCs now come with built-in networking capabilities, enabling seamless communication between various devices and systems. This integration is crucial for the implementation of IoT in industrial settings, allowing for real-time data exchange and remote monitoring. By connecting sensors, machines, and control systems, PLCs facilitate a more interconnected and responsive production environment.
-
Data-Driven Decision Making: The ability to collect, process, and analyze data in real-time is a hallmark of Industry 4.0. PLCs play a crucial role in this by gathering data from various sources and feeding it into data analytics platforms. This data-driven approach helps in predictive maintenance, process optimization, and quality control, thereby enhancing overall operational efficiency.
-
Flexibility and Scalability: Modern PLCs are designed to be highly adaptable, allowing for easy reconfiguration and expansion. This flexibility is essential for industries looking to innovate and adapt to changing market demands quickly. Whether it’s modifying production lines or scaling operations, PLCs provide the necessary agility to meet these challenges.
-
Improved Safety and Reliability: Safety is paramount in industrial operations, and PLCs contribute significantly to this aspect. With advanced diagnostic and fault-tolerant features, PLCs help in early detection of issues and ensure safe shutdown procedures. Additionally, the reliability of PLCs minimizes downtime, which is critical for maintaining continuous production flows.
-
Edge Computing and Artificial Intelligence: The integration of edge computing capabilities into PLCs allows for real-time processing of data at the source, reducing latency and improving decision-making speeds. Moreover, incorporating AI algorithms into PLC systems enables predictive analytics and machine learning applications, further enhancing automation and operational efficiency.
Case Studies and Applications
Numerous industries have already witnessed the transformative impact of PLCs within the framework of Industry 4.0. For instance, in the automotive sector, PLCs are used for precise control of robotic arms in assembly lines, ensuring high levels of accuracy and consistency. In the pharmaceutical industry, PLCs manage complex processes such as formulation, packaging, and quality control, adhering to stringent regulatory standards.
Challenges and Future Directions
While PLCs offer immense benefits, their implementation in Industry 4.0 is not without challenges. Issues such as cybersecurity, interoperability, and the need for skilled personnel to manage and maintain these systems are significant concerns. However, ongoing advancements in technology and continuous training programs are addressing these challenges.
Looking forward, the future of PLCs in Industry 4.0 appears promising. Innovations such as the integration of 5G technology, enhanced AI capabilities, and further advancements in edge computing will continue to push the boundaries of what PLCs can achieve. As industries continue to embrace digital transformation, PLCs will undoubtedly remain a critical component in the quest for increased automation, efficiency, and competitiveness.
Conclusion
In conclusion, Programmable Logic Controllers are at the forefront of the Industry 4.0 revolution, driving significant advancements in industrial automation. Their ability to enhance connectivity, facilitate data-driven decision-making, and provide flexibility and reliability makes them indispensable in modern manufacturing environments. As technology continues to evolve, PLCs will play an even more crucial role in shaping the future of industrial operations, ensuring that industries can meet the demands of an increasingly complex and competitive market.
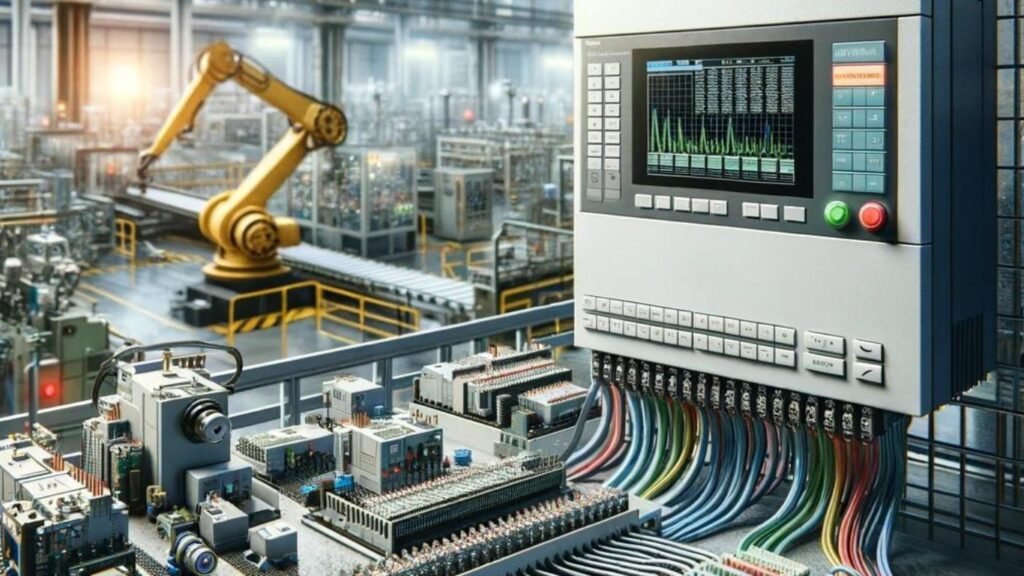